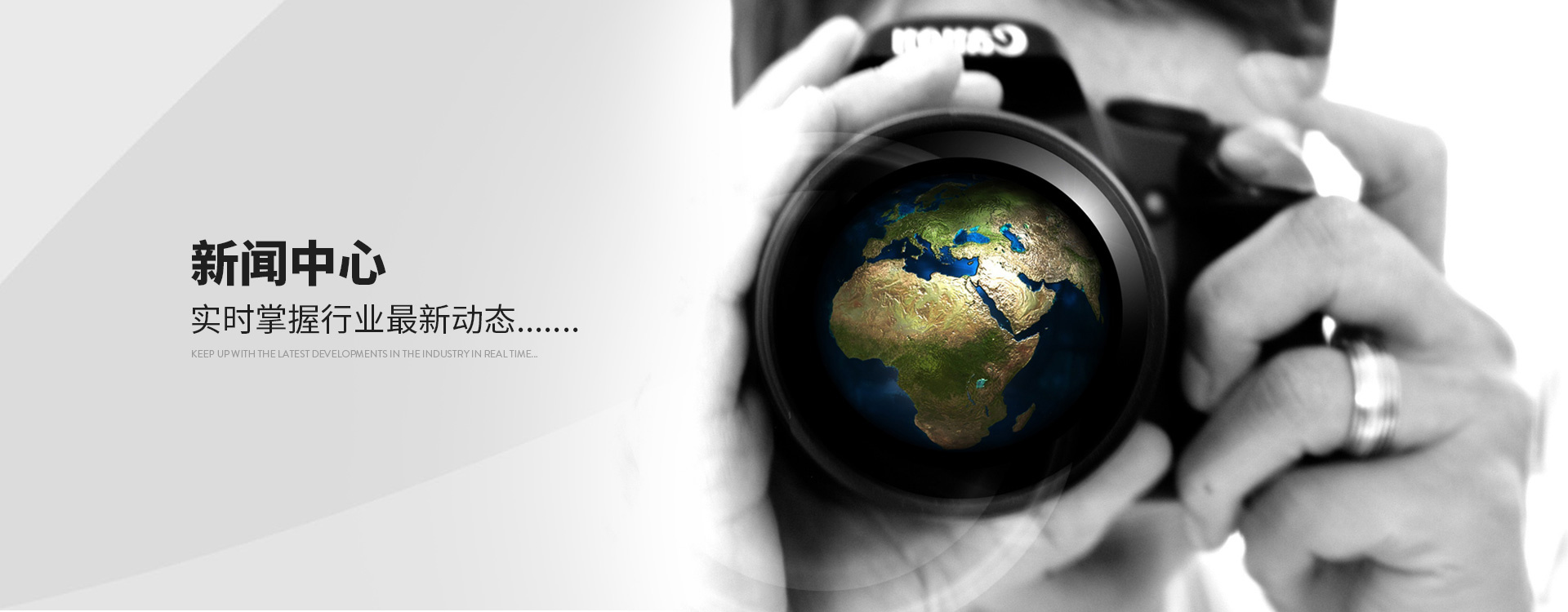
在生產(chǎn)運營效率優(yōu)化方面,人員定位系統(tǒng)如何實現(xiàn)精準調(diào)度
在生產(chǎn)運營效率優(yōu)化中,人員定位系統(tǒng)通過“數(shù)據(jù)感知-智能分析-動態(tài)調(diào)度”的閉環(huán)機制實現(xiàn)精準調(diào)度,核心在于將人員實時位置、技能屬性、任務(wù)優(yōu)先級與生產(chǎn)流程深度融合。以下從技術(shù)邏輯、實施路徑和量化價值三方面展開說明:
一、精準調(diào)度的技術(shù)實現(xiàn)邏輯
1. 人員能力數(shù)字化建模
- 技能標簽體系:將人員技能拆解為可量化指標(如焊接精度等級、設(shè)備調(diào)試經(jīng)驗值、安全操作認證),形成人員能力矩陣。
- 示例:某汽車工廠將焊工技能分為5級,1級僅能操作點焊機,5級可處理機器人弧焊編程。
- 歷史行為畫像:通過定位軌跡和任務(wù)完成記錄,分析人員效率特征(如某員工在A產(chǎn)線效率比B產(chǎn)線高30%)。
2. 生產(chǎn)需求動態(tài)感知
- 任務(wù)優(yōu)先級分級:結(jié)合訂單緊急度、設(shè)備故障等級、質(zhì)量要求劃分任務(wù)優(yōu)先級(如P0-P3級)。
- 示例:某電子廠將新品試產(chǎn)任務(wù)設(shè)為P0級,需優(yōu)先分配5級技能人員;常規(guī)返工任務(wù)設(shè)為P3級,可由3級技能人員處理。
- 資源沖突預警:實時監(jiān)測設(shè)備、工裝、人員等資源占用狀態(tài),提前識別潛在瓶頸。
3. 智能調(diào)度算法引擎
- 多目標優(yōu)化模型:基于任務(wù)優(yōu)先級、人員能力、位置距離、疲勞度等約束條件,構(gòu)建調(diào)度算法。
- 核心公式:
最優(yōu)調(diào)度=argmin人員?(α?技能匹配度+β?距離成本+γ?疲勞系數(shù))
(α,β,γ為權(quán)重參數(shù),通過歷史數(shù)據(jù)訓練得出)
- 核心公式:
- 動態(tài)重調(diào)度機制:當突發(fā)任務(wù)插入或人員離崗時,10秒內(nèi)重新計算最優(yōu)調(diào)度方案。
二、精準調(diào)度的實施路徑
1. 數(shù)據(jù)采集層:構(gòu)建全域感知網(wǎng)絡(luò)
- 定位設(shè)備部署:
- 工廠場景:UWB基站覆蓋產(chǎn)線,定位精度±10厘米,實時更新人員位置。
- 戶外場景:GPS+LoRa組合定位,確保運輸車輛/巡檢人員軌跡連續(xù)。
- 傳感器融合:
- 結(jié)合工牌加速度傳感器監(jiān)測人員疲勞度(如連續(xù)工作4小時后觸發(fā)強制休息提醒)。
- 通過設(shè)備IoT數(shù)據(jù)感知任務(wù)進度(如某機床加工完成率達90%時,自動推送接料人員調(diào)度指令)。
2. 數(shù)據(jù)處理層:建立調(diào)度知識庫
- 歷史調(diào)度數(shù)據(jù)清洗:提取任務(wù)類型、人員分配、完成時間等特征,訓練調(diào)度預測模型。
- 實時調(diào)度規(guī)則引擎:
- 規(guī)則1:P0級任務(wù)優(yōu)先分配5公里內(nèi)且技能匹配度>80%的人員。
- 規(guī)則2:同一人員連續(xù)執(zhí)行高強度任務(wù)(如精密裝配)3小時后,禁止再分配P0級任務(wù)。
3. 執(zhí)行反饋層:閉環(huán)優(yōu)化調(diào)度策略
- 調(diào)度指令推送:通過工牌震動/語音提醒、移動端APP推送任務(wù)指令,10秒內(nèi)確認率達95%。
- 執(zhí)行效果評估:對比實際完成時間與預測值,動態(tài)調(diào)整算法權(quán)重(如某產(chǎn)線實際效率比預測低15%,則增加疲勞系數(shù)權(quán)重)。
三、精準調(diào)度的量化價值
1. 任務(wù)響應效率提升
- 緊急任務(wù)分配時間:從人工調(diào)度平均15分鐘縮短至系統(tǒng)自動分配20秒內(nèi)。
- 設(shè)備停機恢復時間:某機械廠通過定位系統(tǒng)快速調(diào)度技能人員,設(shè)備停機時間從4小時降至1.2小時。
2. 人員利用率優(yōu)化
- 技能匹配率:從人工分配的68%提升至系統(tǒng)自動分配的92%(某電子廠案例)。
- 日均無效走動距離:通過路徑優(yōu)化算法,人員日均無效走動減少42%(某汽車工廠數(shù)據(jù))。
3. 生產(chǎn)質(zhì)量改善
- 次品率下降:某精密儀器廠將技能人員與高精度任務(wù)精準匹配,次品率從3.2%降至0.8%。
- 返工成本降低:某服裝廠通過快速調(diào)度經(jīng)驗人員處理復雜工序,返工成本下降35%。
四、典型場景案例
案例1:汽車工廠焊裝產(chǎn)線調(diào)度
- 問題:某車型焊接工序需5級技能人員,但人工調(diào)度常導致低技能人員占用關(guān)鍵工位。
- 解決方案:
- 部署UWB定位系統(tǒng),實時監(jiān)測人員位置和技能等級。
- 當5級技能人員進入產(chǎn)線50米范圍內(nèi)時,自動推送高優(yōu)先級焊接任務(wù)。
- 效果:
- 關(guān)鍵工位技能匹配率從71%提升至98%。
- 單車焊接時間從42分鐘縮短至35分鐘,產(chǎn)能提升16%。
案例2:電子廠SMT貼片線調(diào)度
- 問題:突發(fā)設(shè)備故障時,需從其他產(chǎn)線調(diào)度技能人員,人工協(xié)調(diào)耗時30分鐘以上。
- 解決方案:
- 建立人員技能-設(shè)備型號匹配數(shù)據(jù)庫,定位系統(tǒng)實時更新人員位置。
- 設(shè)備故障時,系統(tǒng)10秒內(nèi)篩選出5公里內(nèi)且技能匹配度>90%的人員,推送搶修任務(wù)。
- 效果:
- 設(shè)備故障平均恢復時間從2.8小時降至1.1小時。
- 月度設(shè)備OEE(綜合效率)從78%提升至89%。
五、實施建議
- 優(yōu)先場景選擇:
- 高技能依賴工序:如精密裝配、設(shè)備調(diào)試、復雜焊接等。
- 高變化性任務(wù):如新品試產(chǎn)、緊急訂單插入、設(shè)備故障搶修等。
- 技術(shù)選型要點:
- 室內(nèi)定位:UWB(精度) vs 藍牙AOA(成本) vs 超寬帶+慣性導航(復雜環(huán)境)。
- 調(diào)度算法:基于規(guī)則的專家系統(tǒng) vs 強化學習(需大量歷史數(shù)據(jù)訓練)。
- 數(shù)據(jù)安全保障:
- 對人員位置、技能等敏感數(shù)據(jù)加密存儲,權(quán)限分級管理(如僅生產(chǎn)主管可查看技能等級)。
總結(jié):精準調(diào)度的核心價值
人員定位系統(tǒng)通過將人員能力數(shù)據(jù)化、生產(chǎn)需求動態(tài)化、調(diào)度決策智能化,實現(xiàn)從“經(jīng)驗驅(qū)動”到“數(shù)據(jù)驅(qū)動”的效率躍遷。其核心優(yōu)勢在于:
- 減少決策延遲:將調(diào)度響應時間從分鐘級壓縮至秒級。
- 提升資源適配度:將人員技能與任務(wù)需求匹配度從60%提升至90%以上。
- 釋放隱性產(chǎn)能:通過動態(tài)調(diào)度減少15%-30%的無效等待和重復走動時間。
企業(yè)部署建議:
- 試點驗證:選擇1-2條產(chǎn)線進行3個月試點,量化ROI后再全廠推廣。
- 系統(tǒng)對接:與MES、ERP等現(xiàn)有系統(tǒng)集成,避免數(shù)據(jù)孤島。
- 持續(xù)優(yōu)化:定期根據(jù)生產(chǎn)變化(如新品導入、技能培訓)更新調(diào)度規(guī)則和算法權(quán)重。